FAQ
THE WHEEL
There are many factors that need to be taken into account when selecting the best wheel for your needs. To understand more about what those factors are and what options would be the best for you continue reading below.
Different tread materials
Different applications require different tread materials. The possibilities are huge and highly depend on the customers’ expectations, applications, flooring, etc., which makes it difficult to give general advise about different tread materials.
- Polyurethane (flat & convex); great compromise between push and pull forces and ground pressure with medium shore hardness around A92 is in most cases your best choice.
- Polyamides give you the lowest push and pull forces due to hard tread material and shore hardness of D75. Ground pressure is very high and only recommended with extra heavy loads where a low overall height is required. Check your flooring before choosing PA material because high and concentrated ground pressure may leave wheel ruts and may damage expensive flooring. Keep in mind that once the equipment is rolling it may be difficult to stop safely.
- Rubber is probably the most well known tread material. It’s a noise-free movement and has the highest push and pull forces and the lowest ground pressure with shore hardness around A67. The load capacity of rubber is usually lower than of any other material. It is great for transporting sensitive equipment, as it provides a cushioned ride.
Also consider possible resistance against oils, chemicals and metal debris depends on the wheel and time of exposure.
Offset
The larger the offset the lower the swivel resistance; a large offset increases the swivel radius and may cause interference with other components or may stick out too far and possibly hurt workers or cause injuries.
Single or twin wheel
In cases where a low overall height is required in combination with a high load capacity a twin wheel will be the best choice. The main advantage is to reduce the swivel resistance. A single wheel stays in place and the caster swivels around it, it causes high friction and therefore a greater resistance. Using a twin wheel, the wheels are turning in opposite direction, while the caster swivels around, which reduces ground friction to a minimum and gives greater performance.
Wheel diameter
The most significant impact on resistance is the wheel diameter. For loads greater than 1,000kg, we highly recommend using a 160mm or larger wheel diameter to maneuver the equipment safely. The general rule applies to most situations:” The higher the load, the bigger the wheel diameter should be.”
UNDERSTANDING WHEEL MATERIAL
- Polyurethane:
- Injected – highly automated with minium labor cost; the process is also much shorter; Mostly used in the institutional, industrial and medical segment (UAP, XSX, etc)
- Poured – only available for Heavy Duty wheels; poured around a steel or aluminum hub; the process is mostly manual and cost intensive. A glue creates a special bond between the wheel centre and PU tread. (ITP, ETP, FTP, etc.)
In any case, PU gives the end user under normal circumstances great performance with very low roll and swivel resistances (compared to rubber or TENTEprene).
- TENTEprene: Synthetic rubber material; under-injected with the wheel centre; Load capacity lower than PU. Mostly used in the institutional segment. Typical wheels are PJO and PJP.
- Polypropylene (PP): Low density Polymer; Better price point than PA; Lower load capacity than PA; Mostly used in the industrial segment. (POO, POR, etc).
- Polyamide (PA): High density Polymer with high load capacity; Very low roll and swivel resistance; most commonly used in the industrial and heavy duty segment; (UOO, UOR, etc).
- Rubber: Soft rubber material with low to medium load capacity; Institutional and Industrial segment; Smooth and easy rolling with higher start-up force. (PVR, DVR, DIK, etc).
- Elastic Tyre: High-quality elastic tires used in Institutional and Industrial; Tyre is usually press on the wheel centre (UER, UFR, JFX, etc)
- Noise Reduced: Special wheels with a soft core and hard tread. HUR = hard centre, soft layer, hard tread; UOT & POS = shock-absorbing wheel centre / bearing with hard tread.
- Silicon: Silicon tread is only used for applications that have to be resistant to extremly high temperatures Carts for bakery ovens are the most common application. Makes only sense in combination with a stainless steel housing; Industrial segment only.
- Duroplast: An alternative to the more expensive Silicon material; Heat resistant but very hard tread material
CALCULATING THE LOAD CAPACITY
Load capacity is one the determining factors when choosing the right caster for a customers’ application. All load capacities on our website and catalog are dynamic load capacities, which means the caster or wheel is moving with a certain speed and was tested according to EN industry norms and standards.
Factors that play a role for the load capacity are the construction of the housing, wheel material, tread material and shore hardness, mounting plate and bearing type. Rule of thumb is, the larger the wheel diameter the higher the load capacity and the easier it is to move the equipment.
We, as TENTE, recommend our customers to calculate the load rating by using the following formula:
(Tara Weight of Unit + Maximum Load) : 3 = Load Capacity / Castor
The reason for only using three casters is, that one can always lose contact with the ground due to uneven floors. It’s a safety precaution.
CHOSING A WHEEL BEARING
Besides the tread, wheel diameter and swivel bearing, the wheel bearings determine how smooth a caster will travel and thus the quality of the castor.
- Plain bearing: The simplest form of wheel bearing are plain or friction bearings. They are shock-resistant, mostly maintenance free and depending on the material properties also corrosion proof. We recommend plain bearings for wheels on equipment to be moved with low velocity over short distances
- Roller bearing: Besides the fricition and deep groove ball bearings, this robust type of shock-resistant bearing is mainly use for transport equipment castors. Roller bearings are characterised by their low installation height, relatively low roll resistance and high load capacity. The travelling speed of wheels with roller bearings should not exceeed 4 km/h (around walking speed).
- Cone ball bearing: Cone bearings are one of the most imporant groups of roller bearings. Their special advantage when compared to plain bearing is that they lie in a sphere, which provide improved rolling properties.
- Precision ball bearings: The various designs of single row radial precision ball bears to DIN are the highest quality type of bearings. Wheels with these ball bearings have extremely low roll resistance for maximum laod.
Can’t find what you’re looking for? We can help! Give us a call on +44 (0) 1733 578 111 or email us
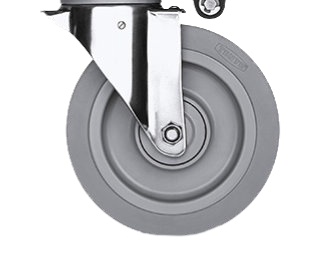